At the U.K.’s prestigious University College London Institute of Healthcare Engineering, professor Rebecca Shipley recently became alarmed. Because COVID-19 can quickly infect the respiratory system, and with so many patients requiring breathing assistance, it was clear that hospitals would run out of ventilators long before the virus spread had peaked.
As she talked through the problem with colleagues one evening, they recognized that some 50% of patients with breathing difficulties did not need invasive ventilators and sedation. The team hit upon the idea of improving an off-patent design for a continuous positive airway pressure device. It involves using a mask that fits around the mouth and nose rather than a tube requiring insertion via the nose or mouth. Regulatory approval was soon obtained, but it still needed to be made quickly and in sufficient quantities to keep the stock of invasive ventilators aside for those truly needing them, in order to save many lives.
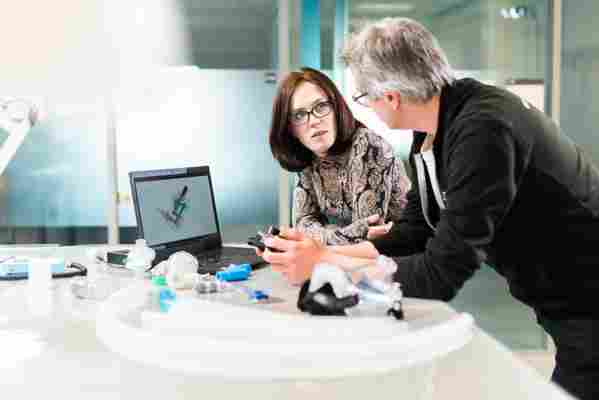
Professor Rebecca Shipley at University College London Institute of Healthcare Engineering.
Enter Mercedes-AMG High Performance Powertrains, the engine division of the Mercedes Formula One team, based in Brixworth, Northamptonshire. The site is one of the leading locations in the world for vehicle design, machine learning, lightweight construction, and other pioneering technologies. Within days, Mercedes had made 100 continuous positive airway pressure devices for testing. Mercedes now stands ready to produce 1,000 a day.
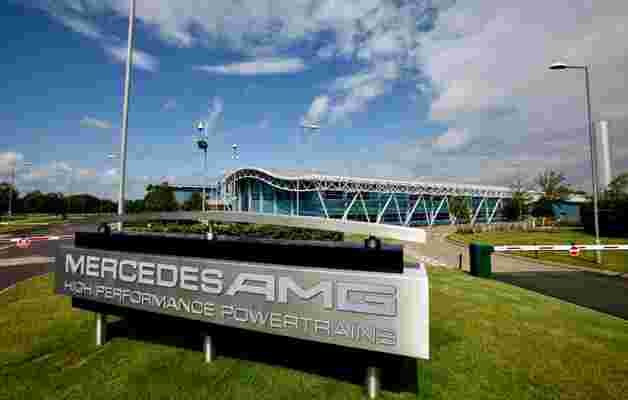
The Mercedes-AMG facility in Brixworth, Northamptonshire.
The Mercedes facility forms part of an elite group of engineering companies located in the U.K.’s Motorsport Valley. Their forte is rapid turnaround of projects. Having only known intense rivalry on the track, these teams are now collaborating during the cancelled Formula One season on Project Pitlane, whose goal is to supply hospital ventilators and other medical devices. Just as in Formula One competition, time is the most precious commodity when it comes to fighting a global pandemic.
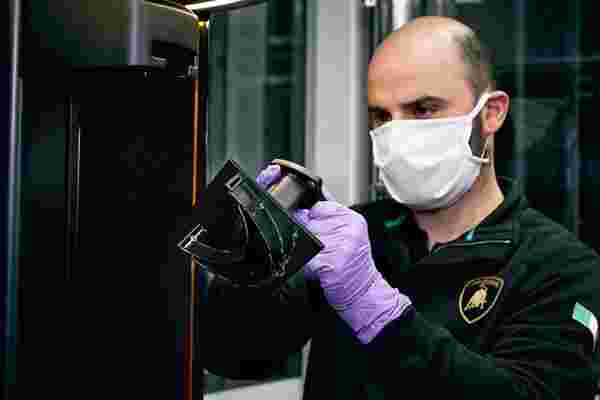
The 3D printing of components for Lamborghini medical shields at Sant’Agata Bolognese, Italy.
Meanwhile, in Italy—a country that has been among the hardest hit by COVID-19—Lamborghini is converting departments of its super sports car production plant at Sant’Agata Bolognese to enable it to make surgical masks and protective plexiglass shields. The masks will be donated to the Sant’Orsola-Malpighi Hospital, in Bologna, an early virus hot spot.
The saddlery that usually outfits the interiors of these super cars is being repurposed to produce 1,000 masks a day, and an additional 200 medical shields are being made using 3D printers in the carbon fiber production plant and the research and development department.
Ford is working with GE Healthcare to make an extra 50,000 ventilators in the next 100 days.
On the other side of the Atlantic, Ford’s president and CEO, Jim Hackett, challenged Ford’s designers and engineers to be “scrappy and creative.” The company is making face shields at the rate of more than 100,000 a week, while partnering with 3M to increase the production of powered air-purifying respirators. Ford is also increasing production of GE Healthcare ventilators with the goal of making an extra 50,000 ventilators in the next 100 days.
The approach exemplifies the partnerships with existing medical equipment makers to reduce cycle times from years to just weeks or even days. Just outside Seattle, an early COVID-19 hot spot, medical device company Ventec Life Systems is partnering with General Motors. And in New York State, now the national virus epicenter, Tesla is on the brink of bringing its Gigafactory 2 manufacturing facility back online to make ventilators for Medtronic, another medical device company. To borrow an industry term, these vital initiatives around the globe are arriving on a just-in-time basis.
Tesla’s Gigafactory 2 facility, Buffalo, New York.